Häufige Fehler und Lösungen beim Schneiden in der Produktionslinie zum Schneiden von Siliziumstahlblechen
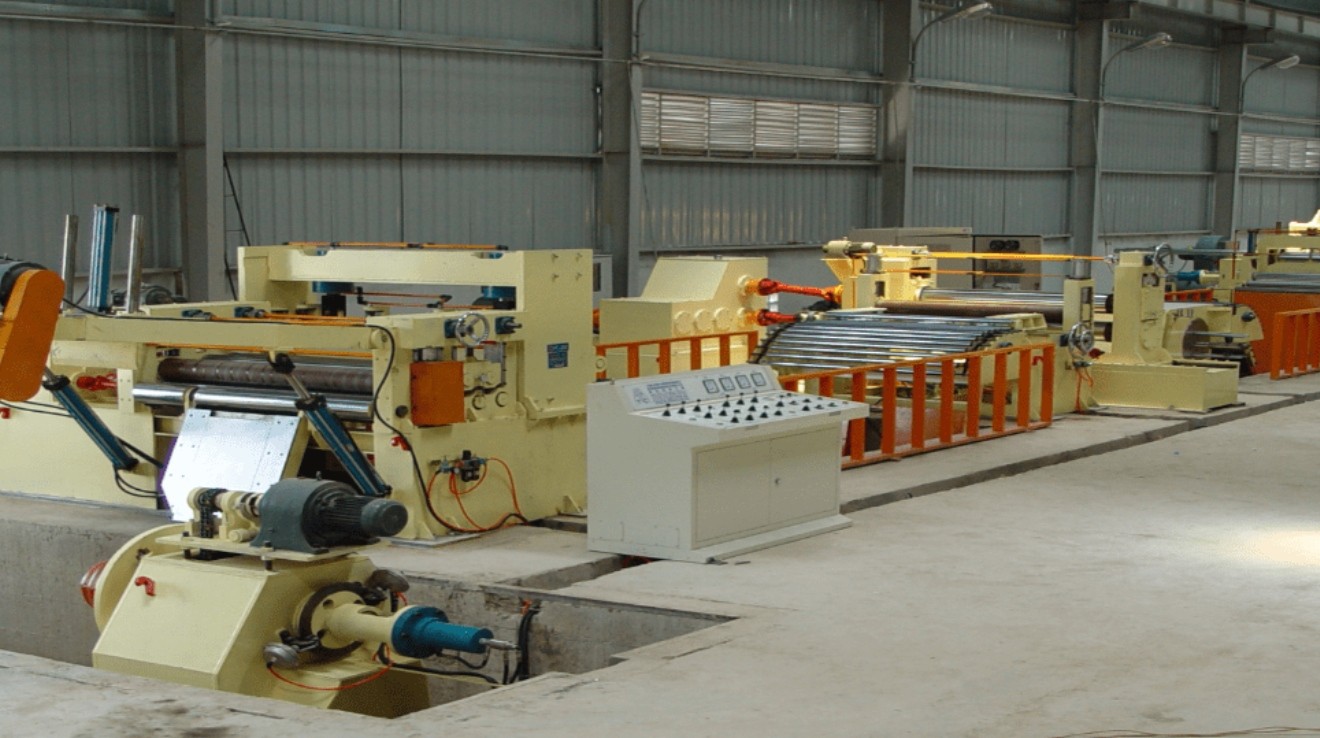
Die Schneideanlage für Siliziumstahlbleche schneidet das Siliziumstahlblech der angegebenen Breite in die benötigten Streifen mit der erforderlichen Breite für das Querschneiden der laminierten Bleche. Die Anlage hierfür ist die Schneideanlage. Die Schneideanlage besteht im Wesentlichen aus einem Zuführ-Abwickler, einer Führungsvorrichtung, einer Walzenschere, einer Prüfvorrichtung, einem Spanntisch, einer Empfangsmaschine, einem Be- und Entladewagen usw.
Bei unsachgemäßer Einstellung von Geräten kommt es während der Nutzung zu Störungen in der Produktionslinie, die zu Produktschäden führen können. Im Folgenden stellen wir kurz häufige Fehlerphänomene, Ursachen und Lösungen vor.
Häufige Fehler, Ursachen und Lösungen
Die Streifenbreite ist instabil.
Dieses Phänomen wird dadurch verursacht, dass der Fräser an der Fräserwelle der Walzenschere nicht befestigt ist. Stoppen Sie die Maschine, um den Fräser zu überprüfen, und ziehen Sie ihn nach der Einstellung fest, um einen Streifen mit der richtigen Stückbreite auszuschneiden.
Streifenmaterial-Frässtifte übertreffen den Standard
1. Der Streifengrat überschreitet den Standard nach dem Rollscheren. Die Hauptgründe dafür, dass der Streifengrat den Standard nach dem Rollscheren überschreitet, sind folgende:
(1) Die Schneide des Werkzeugs ist nicht scharf, und die Grate auf dem Streifen sind durchgehend. Wenn die Schneide defekt ist, äußert sich dies in intermittierenden hellen Flecken auf den Graten des Streifens. An diesem Punkt sollte das Werkzeug nachgeschärft werden.
(2) Bei großem Werkzeugspalt oder großer Überlappung erscheinen die Grate auf dem Streifen durchgehend und es kommt zu einem leichten Aufwölben. In diesem Fall muss die Maschine zur Überprüfung angehalten und der Werkzeugspalt neu eingestellt werden.
2. Die Grate des durch die Spannvorrichtung laufenden Bandes überschreiten den Standard. Wenn die Grate des durch die Spannvorrichtung laufenden Bandes den Standard überschreiten, liegt dies meist daran, dass das Band während des Betriebs seitlich auf die Isolierplatte drückt. Dafür gibt es zwei Gründe:
(1) Die Ebenheit der Isolierscheibe und die Geradheit der Welle, auf der die Isolierscheibe montiert ist, sind nicht gut. Der Rundlauf der Isolierscheibe ist beim Drehen zu groß, wodurch der Streifen die Isolierscheibe während des Betriebs seitlich zusammendrückt. Überprüfen Sie in diesem Fall die Ebenheit der Isolierscheibe und die Geradheit der Welle, auf der die Isolierscheibe montiert ist. Passen Sie sie dann so an, dass der Rundlauf der Isolierscheibe weniger als 1 mm beträgt und der Abstand zwischen den Scheiben durch geeignetes Einstellen des Abstands vermieden werden kann.
(2) Wenn die lokale Dicke des Streifens leicht unterschiedlich ist, kann dies dazu führen, dass der auf der Spannvorrichtung platzierte Airbag den lokalen Druck ungleichmäßig erzeugt, sodass der laufende Streifen während dieses Vorgangs die Isolierplatte seitlich zusammendrückt. In diesem Fall sollten die oberen und unteren Druckplatten am Airbag angepasst, die Anordnung geändert und die Anzahl der Druckplatten erhöht oder verringert werden, um den lokalen Druck des Airbags auszugleichen.
3. Die Biegung des Streifens führt dazu, dass die Geradheit des Streifens nach dem Scheren größer als 0,2 mm/2 m ist. Dafür gibt es hauptsächlich folgende Gründe:
(1) Die Pressplatte an der beweglichen Führung vor der Schneidemaschine ist zu eng, was zu einer Verbiegung des Streifens führen kann. Der Pressgrad der oberen Pressplatte der beweglichen Führung sollte so eingestellt werden, dass zwischen der oberen und unteren Pressplatte ein gewisser Abstand besteht und das Siliziumstahlblech reibungslos hindurchlaufen kann.
(2) Die obere Walze der Antriebsrolle ist nicht parallel zur unteren Walze, was zu einer Abweichung des Bandes während des Betriebs und zu einer Verbiegung des Bandes führt. Die Buchsen an den Zylindern auf beiden Seiten der Antriebsrolle sollten so eingestellt werden, dass die obere Antriebsrolle parallel zur unteren Antriebsrolle verläuft. Dadurch weicht das Band während des Betriebs nicht ab und ein Verbiegen des Bandes kann vermieden werden.
4. Die Streifen werden nicht gleichmäßig gesammelt. Die Streifen werden nicht gleichmäßig gesammelt, was bedeutet, dass die Stirnflächen der Streifen nach dem Sammeln durch den Wickler nicht sauber sind und die Abweichung über ± 2 mm liegt. Dieses Phänomen hat häufig folgende Ursachen:
(1) Die Spulensammelschiene des Wicklers und die Führungsrollensammelschiene der Spannvorrichtung verlaufen nicht parallel zueinander. Dadurch entsteht ein Winkel, der das Band beim Aufwickeln auf den Wickler in eine Richtung ablenkt und die Bandoberfläche uneben macht. Um dieses Phänomen zu beheben, sollte die Position der Führungsrolle der Spannvorrichtung so eingestellt werden, dass die Spulensammelschiene des Wicklers und die Führungsrollensammelschiene des Spanners parallel zueinander verlaufen.
(2) Wird der Streifen nicht gerade in die Klemmnut des Wicklers eingeführt, wird er zu Beginn des Wickelns versetzt. Nach einigen Versatzumdrehungen findet der Streifen automatisch seine Position. Anschließend können die Streifen entnommen werden.
(3) Die Spule selbst ist ungleichmäßig und hat eine ungleichmäßige Dicke. Nach dem Schneiden in Streifen wird die Kantenspannung ungleichmäßig freigesetzt. Wenn das Teil durch die Spannvorrichtung zusammengedrückt wird, führt die gleichmäßige Zugkraft dazu, dass die Streifen ungleichmäßig werden. Daher sollte der Druckteil der Spannvorrichtung entsprechend den tatsächlichen Bedingungen der Streifen eingestellt werden, damit die Streifen nach der Einstellung ordnungsgemäß gesammelt werden können.
Abschließend
Ob die Produkte nach dem Schneiden die Anforderungen des nächsten Prozesses erfüllen, hängt maßgeblich von der Vertrautheit des Bedieners mit der Anlage und der rechtzeitigen Anpassung der Anlage ab. Normalerweise kann der Bediener nach einer gewissen Nutzungsdauer der Schneidanlage die Leistung der Anlage verstehen und sie während des Betriebs rechtzeitig anpassen, um die Ausfallrate zu reduzieren und die Produktanforderungen zu erfüllen. Bei Fragen oder beim Kauf von Schneiddraht kontaktieren Sie uns bitte.
Hengli ist ein professioneller Hersteller von kundenspezifischen Siliziumstahl-Schneideanlagen . Zu den Hauptprodukten zählen Siliziumstahl-Schneideanlagen, Längsschneider, Automatisierungssysteme für das Stanzen und Formen von Automobil-Außenhautteilen, Online-Roboter, hochpräzise automatische Blechschneideanlagen, industrielle Automatisierungssysteme für die Online-Inspektion, elektrische Automatisierungsgeräte und umfassende Lösungen für die Automatisierungssteuerung. Die Hauptprodukte sind auf weltweit fortschrittliche Technologien abgestimmt und finden breite Anwendung in wichtigen Branchen der Volkswirtschaft, wie z. B. Automobilbau und -teileverarbeitung, Eisen- und Stahlmetallurgie, Stromerzeugung und Metallverpackung.