Industrielle Anwendung der Transformatorkern-Produktionslinie
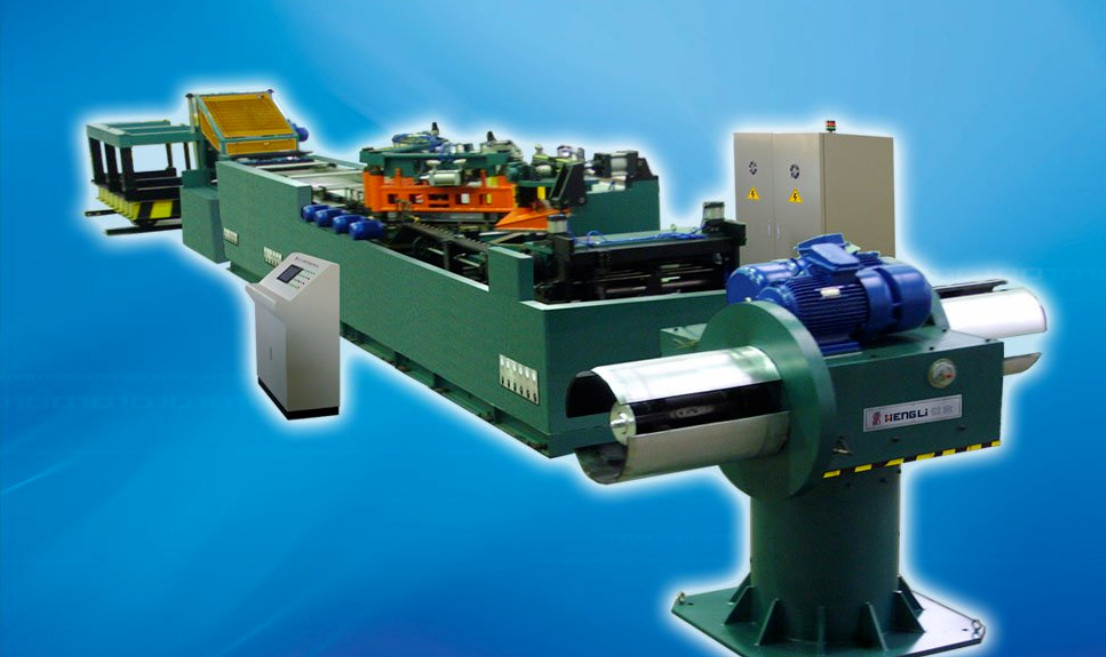
Transformatoren sind Schlüsselkomponenten in verschiedenen Branchen und ermöglichen die effiziente Übertragung und Verteilung elektrischer Energie. Hinter jedem funktionsfähigen Transformator verbirgt sich ein sorgfältig konstruierter Kern, der die Grundlage seines Betriebs bildet. Transformatorkern-Produktionslinien finden vielfältige industrielle Anwendungen und sind für den reibungslosen Betrieb von Stromverteilungsnetzen weltweit unerlässlich.
Die Bedeutung des Transformatorkerns
Die Bedeutung von Transformatorkernen in der Produktion von Stromnetzen liegt darin, dass sie als kritische Komponenten für die Stromübertragung und -verteilung fungieren. Diese Kerne sind entscheidend für die Spannungswandlung, ermöglichen eine effiziente Stromübertragung im Netz und erleichtern den Betrieb verschiedener elektrischer Geräte und Maschinen. Indem sie einen magnetischen Pfad für den elektrischen Fluss bereitstellen, gewährleisten Transformatorkerne eine effiziente Energieumwandlung und unterstützen so die Funktionen von Kraftwerken, Umspannwerken und Industrieanlagen. Ihre Bedeutung erstreckt sich auch auf die Spannungsregelung, die Impedanzanpassung und die Minimierung von Leistungsverlusten während der Übertragung und trägt so zur allgemeinen Zuverlässigkeit und Stabilität des Netzes bei. Transformatorkerne bilden das Rückgrat moderner Strominfrastruktur und ermöglichen die reibungslose Stromversorgung von Haushalten, Unternehmen und Industrien weltweit.
Technologie zur Herstellung von Transformatorkernen
Die Technologie zur Herstellung von Transformatorkernen besteht aus einer komplexen Reihe von Prozessen zur Herstellung der grundlegenden magnetischen Komponenten, die in Transformatoren verwendet werden.
Magnetkern-Schneidtechnologie: Die Magnetkern-Schneidtechnologie umfasst die präzise Formgebung und Größenanpassung von Siliziumstahlblechen, dem Hauptmaterial des Magnetkerns. Moderne Schneidemaschinen mit Computersteuerung und lasergesteuerter Präzision ermöglichen Herstellern die Einhaltung präziser Abmessungen und Toleranzen. Diese Maschinen können große Mengen an Laminatmaterialien verarbeiten und gleichzeitig den Materialabfall minimieren, die Effizienz optimieren und die Produktionskosten senken. Darüber hinaus gewährleistet der automatisierte Schneidprozess die Gleichmäßigkeit und Konsistenz der Kerngeometrie, die für die optimale Magnet- und Transformatorleistung entscheidend ist.
Wickeltechnologie: Unter Wickeltechnologie versteht man das Wickeln einer Spule um den Transformatorkern, um magnetischen Fluss zu erzeugen. Präzisionswickelanlagen ermöglichen Herstellern, enge Toleranzen und gleichmäßige Wickelmuster zu erreichen und so optimale magnetische Kopplung und elektrische Leistung zu gewährleisten. Die automatische Wickelmaschine ist mit einer programmierbaren Steuerung und einem Spannungsregelsystem ausgestattet, um die präzise Platzierung und Ausrichtung der Wicklungsleiter zu gewährleisten. Fortschrittliche Wickeltechniken, wie z. B. mehrlagige und versetzte Wicklungen, minimieren Wirbelstromverluste und erhöhen die Effizienz des Transformators. Darüber hinaus ermöglicht CAD-Software (Computer-Aided Design) Ingenieuren die Optimierung der Wicklungskonfigurationen basierend auf spezifischen Spannungs- und Stromanforderungen und verbessert so die Gesamtleistung und Zuverlässigkeit des Transformators.
Stapeltechnologie: Bei der Stapeltechnologie werden Lamellen zu einer endgültigen Kernstruktur zusammengefügt. Automatisierte Stapelsysteme nutzen Roboterarme und Präzisionsausrichtungsmechanismen, um Lamellen mit Mikrometerpräzision zu stapeln. Das ineinandergreifende Lamellendesign und die Verbindungstechnologie tragen zur Erhaltung der strukturellen Integrität bei und verhindern, dass sich der Kern unter elektromagnetischen Kräften verformt. Fortschrittliche Stapelalgorithmen optimieren die Lamellenausrichtung und die Stapelreihenfolge, um Kernverluste zu minimieren und die Flussdichte zu maximieren. Darüber hinaus reduziert der automatisierte Stapelprozess die Produktionszeit und die Arbeitskosten erheblich und gewährleistet gleichzeitig gleichbleibende Qualität und Leistung von Charge zu Charge.
Zusammenfassend umfasst die Technologie zur Herstellung von Transformatorkernen modernste Verfahren und Anlagen, die für die präzise, effiziente und zuverlässige Herstellung von Hochleistungskernen entwickelt wurden. Durch den Einsatz fortschrittlicher Schneid-, Wickel- und Stapeltechnologien können Hersteller die hohen Anforderungen moderner Transformatoren erfüllen und eine effiziente Energieübertragung und -verteilung unterstützen.
Sicherheitsvorkehrungen bei der Herstellung von Transformatorkernen
Persönliche Schutzausrüstung (PSA): Mitarbeiter, die an der Herstellung von Transformatorkernen beteiligt sind, sollten mit geeigneter persönlicher Schutzausrüstung ausgestattet sein, darunter Schutzbrille, Handschuhe, Gehörschutz und Sicherheitsschuhe mit Stahlkappe. Persönliche Schutzausrüstung trägt dazu bei, die Risiken im Umgang mit schweren Maschinen, scharfen Werkzeugen und potenziell gefährlichen Materialien wie Metallspänen und Öl zu reduzieren. Regelmäßige Schulungen zur richtigen Verwendung und Wartung der PSA sind unerlässlich, um sicherzustellen, dass sie die Mitarbeiter wirksam vor Gefahren am Arbeitsplatz schützt.
Maschinenschutz und Sicherheitsverriegelungen: Maschinen in der Transformatorkernproduktion sollten mit geeigneten Schutzvorrichtungen und Sicherheitsverriegelungen ausgestattet sein, um versehentlichen Kontakt mit beweglichen Teilen und Gefahrenbereichen zu verhindern. Physische Barrieren, Schutzschilde und Not-Aus-Schalter tragen dazu bei, das Verletzungsrisiko während des Betriebs zu minimieren. Regelmäßige Wartung und Inspektion der Maschinenschutzvorrichtungen und -verriegelungen ist entscheidend, um potenzielle Sicherheitsrisiken frühzeitig zu erkennen und zu beheben. Darüber hinaus sollten Mitarbeiter umfassend in Maschinensicherheitsprotokollen und Notfallmaßnahmen geschult werden, um das Unfall- und Verletzungsrisiko zu reduzieren.
Materialhandhabung und Ergonomie: Sachgemäße Materialhandhabungstechniken und ergonomische Aspekte sind entscheidend, um Muskel-Skelett-Verletzungen und Belastungen bei Mitarbeitern vorzubeugen. Schwere Bauteile und Rohstoffe sollten mit geeigneten Hebevorrichtungen wie Gabelstaplern und Brückenkränen gelagert und transportiert werden, um das Risiko von Rückenverletzungen und Muskelzerrungen zu verringern. Arbeitsplätze sollten ergonomisch gestaltet sein, um eine korrekte Körperhaltung zu fördern und Verletzungen durch wiederholte Belastungen zu minimieren. Schulungsprogramme zu sicheren Hebetechniken und ergonomischem Bewusstsein helfen Mitarbeitern, potenzielle ergonomische Gefahren am Arbeitsplatz zu erkennen und zu beheben.
Chemische Sicherheit und Belüftung: Die Herstellung von Transformatorkernen kann Reinigungs-, Bearbeitungs- und Oberflächenvorbereitungsprozesse mit Chemikalien, Schmiermitteln und Lösungsmitteln umfassen. Arbeitgeber müssen strenge Vorschriften für den Umgang mit Chemikalien, ihre Lagerung und Entsorgung einhalten, um das Risiko einer Exposition und Umweltkontamination zu minimieren. Geeignete Belüftungssysteme und Abzugshauben sollten installiert werden, um Luftschadstoffe zu kontrollieren und die Luftqualität innerhalb sicherer Grenzen zu halten. Mitarbeiter sollten über chemische Gefahren, sichere Handhabungsverfahren und Notfallmaßnahmen geschult werden, um das Risiko chemikalienbedingter Verletzungen und Erkrankungen zu verringern.
Durch die Umsetzung umfassender Sicherheitsmaßnahmen und die Förderung einer Kultur des Sicherheitsbewusstseins und der Einhaltung von Vorschriften können Hersteller ein Arbeitsumfeld schaffen, das das Wohlbefinden der Mitarbeiter und die operative Exzellenz in der Transformatorkernproduktion fördert. Regelmäßige Sicherheitsaudits, Gefährdungsbeurteilungen und kontinuierliche Verbesserungsinitiativen sind unerlässlich, um neu auftretende Sicherheitsrisiken zu erkennen und zu minimieren und die langfristige Nachhaltigkeit des Produktionsprozesses zu gewährleisten.
Abschließend
Zusammenfassend lässt sich sagen, dass der industrielle Einsatz von Transformatorkern-Produktionslinien eine entscheidende Rolle für die Zuverlässigkeit, Effizienz und Sicherheit der Energieinfrastruktur in verschiedenen Branchen spielt. Angesichts des technologischen Fortschritts und der steigenden Marktanforderungen müssen Hersteller Innovation und Nachhaltigkeit vorantreiben, um in diesem dynamischen Umfeld erfolgreich zu sein. Wenn Sie mehr erfahren oder eine Transformatorkern-Produktionslinie erwerben möchten, kontaktieren Sie uns bitte.
Hengli ist ein professioneller Hersteller von Transformatorkern-Produktionslinien . Das nationale Hightech-Unternehmen ist auf die Forschung und Entwicklung sowie die Herstellung hochwertiger industrieller Automatisierungsanlagen spezialisiert. Hengli zählt zu den wichtigsten Anbietern von Automatisierungsanlagen für Blechschneiden und -umformen in China. Die Hauptprodukte entsprechen den neuesten Technologien weltweit und finden breite Anwendung in wichtigen Branchen der Volkswirtschaft, wie beispielsweise der Automobilherstellung und -teileverarbeitung, der Stahlmetallurgie, der Stromerzeugung und der Metallverpackung.